Best ERP Solutions for Small Manufacturing Businesses
- Team SB Infotech
- 6 days ago
- 19 min read

Managing a small manufacturing business often involves balancing numerous tasks, from overseeing production schedules to maintaining inventory levels. Staying organized and efficient can be challenging, especially when scaling your operations.
This is where an ERP (Enterprise Resource Planning) system can make a significant difference. By integrating all core business processes into one proper system, ERP solutions can help manage everything from finances to supply chain logistics, improving both productivity and decision-making.
40% of companies identified better functionality as their primary reason for implementing an ERP system, highlighting the importance of enhanced capabilities to manage operations. For small manufacturing businesses, this means fewer errors, faster processes, and reduced costs, ultimately allowing you to focus on growing your business instead of getting hindered in day-to-day management.
In this blog, we'll explore the best ERP solutions for small manufacturing businesses, highlighting the features that matter most. This guide will help you make an informed choice to improve efficiency and drive growth. Let's get started!
What Is ERP and Why Does It Matter for Small Manufacturers?
An ERP (Enterprise Resource Planning) system is a software solution designed to help businesses manage and integrate essential parts of their operations. Whether it's accounting, inventory management, human resources, or production scheduling, ERP brings all these functions under one roof, enabling smooth data flow and process automation.
Think of an ERP system as the central hub that unites the different moving parts of your business. Instead of using multiple software programs or spreadsheets to manage inventory, accounting, and production planning, an ERP connects everything in one cohesive system. It gives small manufacturers the ability to monitor all aspects of their business in real-time, enabling smarter and faster decision-making.
Here's why an ERP system is essential for small manufacturers:
Simplified Operations: Small manufacturers often struggle with managing various operations, such as procurement, production, and sales, in separate systems. This fragmented approach can result in data inconsistencies and delays. ERP consolidates these operations into one platform, allowing your team to work efficiently and access accurate, up-to-date information across the board.
Improved Resource Management: An ERP system helps small manufacturers track their resources, be it raw materials, finished goods, or human resources, more effectively. By automating processes such as inventory tracking and procurement, businesses can minimize waste, optimize resource allocation, and prevent stockouts.
Real-Time Insights: With ERP, small manufacturers gain access to real-time data. This means that business owners and managers can track production, inventory, and financial data at any given moment. This visibility helps identify potential issues before they escalate, enabling data-driven decision-making.
Scalability: As small manufacturers grow, the complexity of their operations increases. ERP systems are scalable, meaning they can grow in line with your business. Whether you're adding new products, increasing production capacity, or expanding into new markets, an ERP system can be customized to accommodate these changes.
Enhanced Collaboration and Communication: With all departments connected through a single platform, communication between teams becomes smoother and more efficient. No more back-and-forth emails, phone calls, or waiting for data from another department. ERP ensures that everyone has access to the same real-time data, promoting better collaboration and faster decision-making.
In India, where many small manufacturers face unique challenges, an ERP system can be a valuable resource. Businesses in regions like Gujarat or Tamil Nadu, often with rapidly growing industries, need tools that support local requirements such as GST compliance.
ERP systems simplify tax calculations and ensure you stay up-to-date with regulatory changes, saving time and avoiding fines. Moreover, affordable ERP tools designed for startups make these systems accessible to manufacturers just starting, helping them compete with larger companies from the outset.
While ERP systems offer core functionalities across the board, the real impact lies in how well they align with your specific industry needs. Let’s take a closer look at how the manufacturing sector plays a role in shaping ERP software choices.
How does Manufacturing Affect ERP Selection?
The manufacturing industry isn’t one-size-fits-all, and your ERP software shouldn’t be either. The needs of a corrugated box manufacturer differ greatly from a precision parts maker or a food processor. That’s why the sector you operate in plays a massive role in choosing the right ERP solution.
Manufacturing companies represent the largest portion of ERP software adoption, with 47% of companies looking to purchase ERP software coming from the manufacturing sector. This highlights the critical need for manufacturers to choose ERP systems that align with their unique industry requirements.
Let’s break this down:
Corrugation & Packaging Businesses need specific ERP capabilities like reel management, dispatch scheduling, and order-based technical specs. For them, flexibility and customization options are crucial since every job might have a different size, board grade, or print requirements.
Textile and Apparel Manufacturers look for color and size variants, batch dye tracking, and vendor management. Their ERP must simplify inventory across multiple SKUs and manage returns and reprocessing effectively.
Process Manufacturers (like those in food, pharma, or chemicals) need ERP systems that support batch tracking, quality control, expiration date monitoring, and strict compliance reporting. These features are essential when working with perishable or regulated goods.
Discrete Manufacturers (like machinery, electronics, or auto parts) require tools that handle BOM (Bill of Materials) management, make-to-order workflows, and multi-level assembly processes. Real-time shop floor tracking and machine data integration also matter a lot here.
Startups or Small Manufacturers often need ERP systems that are affordable, GST-compliant, and cloud-based, especially in regions like Tamil Nadu or Gujarat, where cost and simplicity matters.
Choosing an ERP that fits your industry is not just about getting things done. It’s about making sure your system works with your operations, not against them.
Now let’s take a look at some of the best ERP solutions available for small businesses.
Top 10 ERP Solutions for Small Manufacturing Businesses in 2025
Small manufacturers need an ERP system that understands their processes, works within their budget, and scales as they grow. We’ve picked out five of the best ERP solutions that are not just popular names but actually work for smaller manufacturing units. Each one offers specific strengths depending on your industry, budget, and growth plans.
Here's a look at the top ERP systems to consider in 2025:
SB Infotech
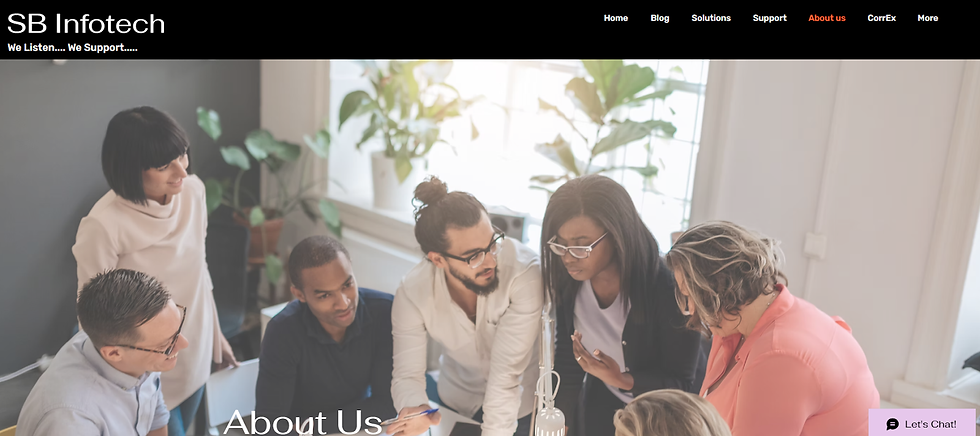
SB Infotech stands out as a leading ERP solution provider for small manufacturing businesses, thanks to its deep industry expertise and customer-centric approach. Specializing in solutions based on Microsoft Dynamics 365 Business Central, SB Infotech delivers customized ERP systems that manage manufacturing operations, enhance customer engagement, and provide real-time insights. With a focus on industry-specific solutions such as corrugation and paper manufacturing, SB Infotech ensures that businesses can optimize their processes and scale effectively.
With their platform, businesses can manage everything from inventory and production to sales and accounting in one unified system. This centralized approach helps manufacturers reduce errors, save time, and gain real-time insights into their operations.
Experience & Expertise
With years of experience in delivering ERP solutions, SBInfo Tech brings a deep understanding of the challenges faced by small manufacturing businesses. As an ISV Partner of Microsoft, SBInfo Tech has extensive knowledge in system customization and integrating business processes with Microsoft technologies. This partnership allows them to offer customized solutions that meet the unique needs of each business, ensuring smooth system integration and long-term support.
Best For:
SBInfo Tech is ideal for small manufacturing businesses that need an easy-to-use and scalable system to manage their operations efficiently. It is particularly well-suited for industries such as:
Manufacturing: Perfect for manufacturers who need to track production schedules, manage inventory, and streamline their supply chain.
Textiles: Assists textile manufacturers in managing orders and stock, ensuring smooth operations.
Electronics: Ideal for electronics manufacturers who require detailed production tracking and inventory management.
Automotive Parts: Helps automotive parts manufacturers streamline their order management, inventory control, and production planning.
Key Features:
Inventory Management: Track stock levels in real-time to minimize waste, avoid stockouts, and ensure smooth operations.
Production Planning: Plan and monitor production schedules to ensure deadlines are met and resources are utilized efficiently.
Sales & Order Management: Integrate your sales processes for accurate order tracking and better customer management.
Financial Management: Handle invoicing, accounting, and financial reporting in one centralized system, ensuring financial accuracy.
Supply Chain Integration: Manage purchase orders, deliveries, and supplier relationships more effectively.
Reporting & Analytics: Access comprehensive reports and real-time insights to support better decision-making.
Quality Control: Conduct thorough quality checks across all stages of production with quality checklists and inspection sheets to ensure products meet the highest standards before leaving the factory.
Subcontracting & Process Automation: Easily manage outsourced tasks with pre-defined process routing and subcontractor management capabilities, reducing manual errors and ensuring a smooth flow of work.
Analytics with Power BI: Integrate Power BI for real-time insights across production and operations. Monitor performance, track key metrics, and drive informed decision-making to enhance productivity and profitability.
CorrEx: Purpose-Built ERP Add-On for Corrugation Manufacturing
CorrEx is a purpose-built solution developed by SB Infotech to meet the unique needs of the corrugation manufacturing industry. Built on Microsoft Dynamics 365 Business Central, CorrEx extends core ERP functionality to include highly specialized modules that support every stage of the corrugation production process. From managing reel inventory and finished goods specifications to dispatch planning and subcontracting operations, CorrEx brings structure, traceability, and efficiency to daily manufacturing workflows.
CorrEx's seamless integration between ERP and MES functionalities makes it stand out, allowing manufacturers to monitor machine-level activity while staying aligned with business objectives like cost control, inventory optimization, and timely delivery. With features like real-time machine integration, detailed process routing, and logistics tracking, CorrEx helps corrugated packaging businesses achieve greater visibility, reduced waste, and higher product consistency within a unified system.
Deployment: Cloud-based ERP, offering flexible, cost-effective access from anywhere.
User Range: Custom (ideal for businesses of all sizes, with flexible configurations that grow as your business does)
Pricing: Custom (based on modules and user count)
NetSuite ERP

NetSuite is often the first serious ERP step for small manufacturers moving beyond spreadsheets and patchy systems. As a cloud-based platform with global reach, it’s known for simplifying core operations without overcomplicating the setup process. For companies in the early stages of scaling, NetSuite offers stability, transparency, and room to grow.
Best for:
Manufacturers outgrow QuickBooks or Zoho, needing real-time financial and operational visibility.
Key Features:
Unified dashboard for operations, inventory, and finances.
Role-based access for different teams.
Real-time visibility and mobile accessibility.
Easy compliance with tax and audit requirements.
Smooth scaling with new users and module additions.
Deployment: Cloud & On-Premise
User Range: 10–Unlimited
Pricing: Starts at $125/user/month
Implementation Cost: $10,000+
SAP S/4HANA Cloud
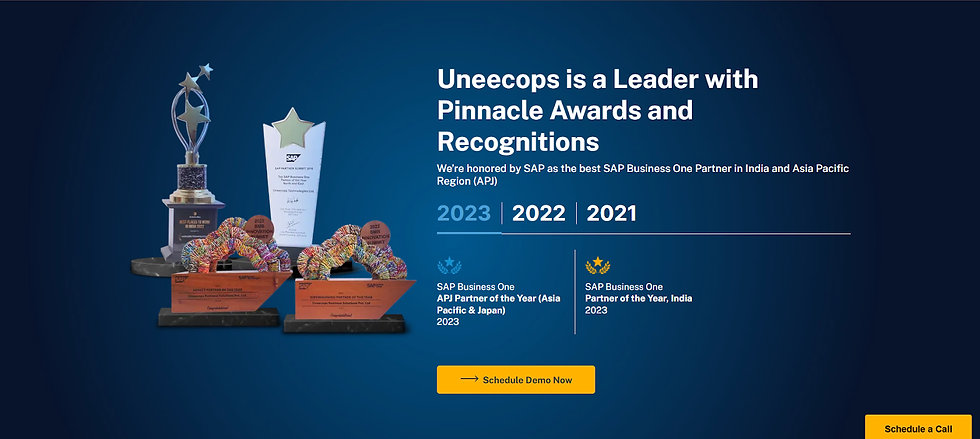
SAP S/4HANA Cloud brings enterprise-grade capabilities into the hands of growing manufacturers. With powerful analytics, AI integrations, and real-time data handling, it's ideal for businesses looking to level up their operations while keeping things organized and efficient.
Best for:
Manufacturers with multi-site operations and high compliance needs, planning for long-term scalability.
Key Features:
Predictive analytics and real-time production monitoring.
Smooth integration with SAP's suite and third-party tools.
Workflow customization for procurement, logistics, and finance.
Comprehensive compliance support for India (GST, e-invoicing).
Deployment: Cloud & On-Premise
User Range: 15–Unlimited
Pricing: Starts at $200/user/month
Implementation Cost: $75,000+
Cetec ERP
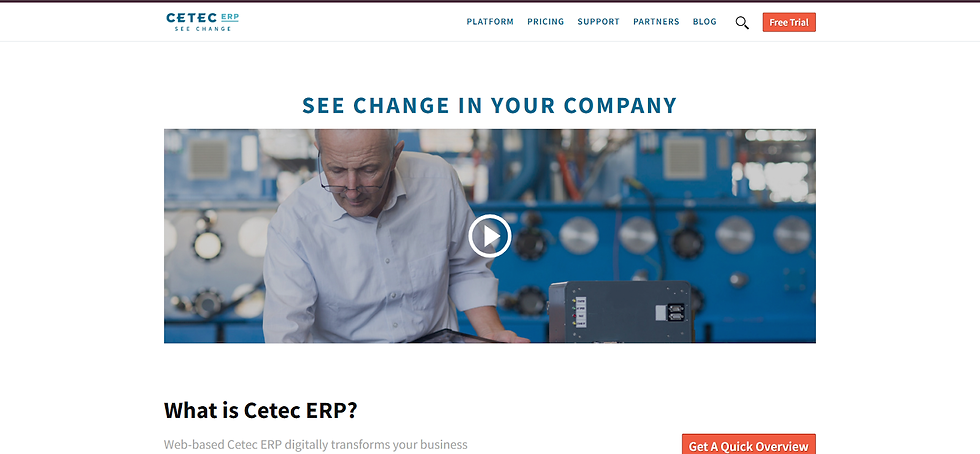
Cetec ERP stands out as one of the most cost-effective and functional ERP solutions for small and mid-sized manufacturers. It's built for companies that want full ERP capabilities without massive upfront investments or IT overhead.
Best for:
Budget-conscious manufacturers are seeking full ERP capabilities with a lean team.
Key Features:
Cloud-native system with mobile and desktop access.
Built-in CRM, quoting, and order tracking.
Inventory and warehouse management with barcode support.
Integrated quality management and audit tracking.
Free implementation for SaaS subscribers.
Deployment: Cloud & On-Premise
User Range: 5–Unlimited
Pricing: Starts at $50/user/month
Implementation Cost: $0 for SaaS users
Sage X3 ERP

Sage X3 offers a middle ground between basic ERPs and enterprise-level platforms. It’s highly adaptable for manufacturers handling multiple product lines, currencies, or facilities. With strong reporting tools and integrations, it’s built to help businesses scale steadily.
Best for:
Mid-sized manufacturers managing complex operations or planning regional/global expansion.
Key Features:
Multi-language, multi-site, and multi-currency support.
Real-time insight into production, purchasing, and inventory.
Customizable workflows for process-specific needs.
Flexible deployment and easy third-party app integration.
Deployment: Cloud & On-Premise
User Range: 10–1000
Pricing: Starts at $75/user/month
Implementation Cost: $100,000+
Acumatica Cloud ERP

Acumatica Cloud ERP offers a modern, scalable solution perfect for manufacturers who want to utilize the power of cloud technology without breaking the bank. Known for its flexibility, Acumatica is designed for mid-sized manufacturers looking to manage operations with advanced technology.
Best for:
Ideal for mid-sized manufacturers who need a flexible cloud-based ERP solution with AI and IoT integrations to improve automation.
Key Features:
Cloud-based ERP with AI & IoT integration
Flexible scalability as business grows
Mobile access for on-the-go management
Inventory management with real-time tracking
Advanced analytics and reporting tools
Deployment: Cloud
User Range: 5–Unlimited
Pricing: Starts at $7.5K - $150K
Implementation Cost: Custom (based on modules and user count)
Infor CloudSuite Industrial

Infor CloudSuite Industrial is a powerful ERP solution designed for discrete manufacturers, offering comprehensive features to smooth operations and enhance efficiency. It supports both cloud and on-premise deployments, making it suitable for businesses that need flexibility and scalability.
Best for:
Medium to large manufacturers in need of flexible, scalable ERP solutions that support complex manufacturing workflows and global operations.
Key Features:
Cloud & On-Premise deployment options.
Real-time production monitoring and tracking.
Comprehensive financial management and reporting tools.
Innovative manufacturing features for improved efficiency.
Customizable workflows with Extend and Evolve components.
Integrated supply chain and inventory management.
Deployment: Cloud & On-Premise
User Range: 5–1000+
Pricing: Starts at $150/user/month
Implementation Cost: $25K - $500K
IFS Cloud
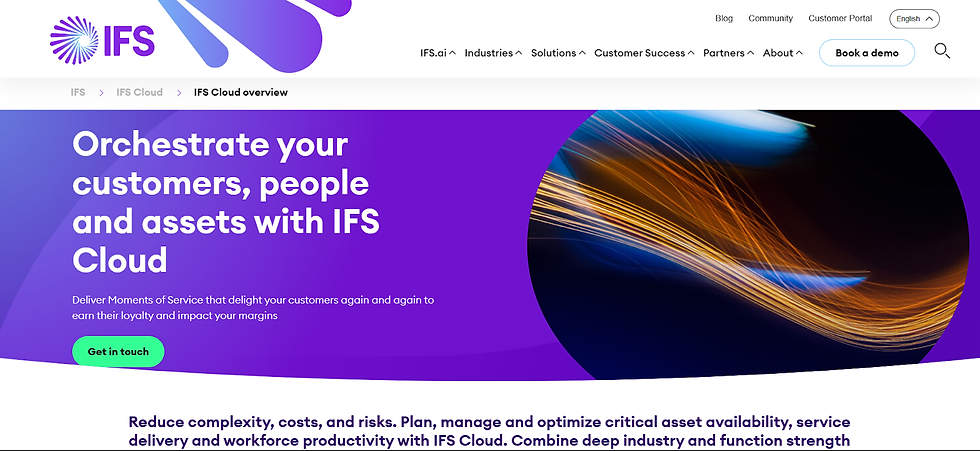
IFS Cloud combines ERP, Enterprise Asset Management (EAM), and Enterprise Service Management (ESM) into a single platform, making it perfect for manufacturers looking for an all-in-one solution to handle both operational and service management needs.
Best for:
Best suited for large-scale manufacturers who need real-time shop floor visibility, asset management, and an integrated solution for production and service management.
Key Features:
Comprehensive ERP + EAM + ESM integration
Real-time production monitoring
Predictive analytics for demand forecasting
Flexible deployment (cloud or on-premise)
Scalable for multi-site operations
Deployment: Cloud & On-Premise
User Range: 100+
Pricing: Custom pricing
Implementation Cost: Custom pricing
DELMIAWorks (IQMS)
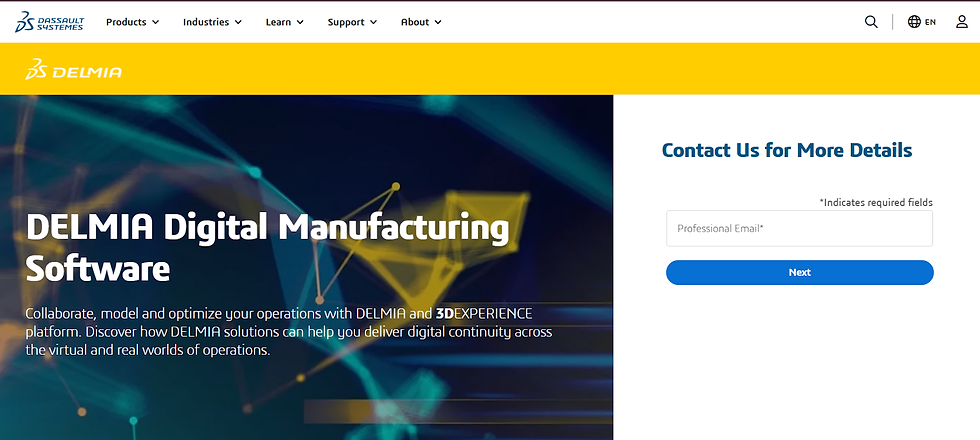
DELMIAWorks (formerly IQMS) offers an integrated ERP and MES (Manufacturing Execution System) solution, providing manufacturers with real-time visibility into production and shop floor processes. It's a powerful tool for manufacturers looking for enhanced control and efficiency.
Best for:
Ideal for process manufacturers needing real-time control over production and businesses looking for a single-vendor solution that integrates ERP and MES.
Key Features:
Integrated ERP and MES in one platform
Real-time shop floor visibility
Unified system for production and business management
Comprehensive quality management
Mobile access for on-the-go monitoring
Deployment: Cloud & On-Premise
User Range: 5–Unlimited
Pricing: Starts at $250/user/month
Implementation Cost: $20,000+
Epicor Kinetic
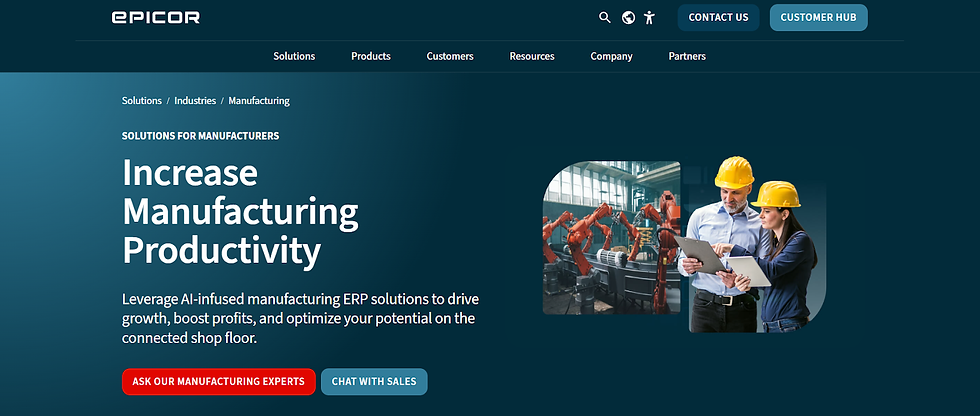
Epicor Kinetic is a flexible ERP system designed for discrete manufacturers. It helps businesses optimize real-time production and quality management while offering the flexibility to adapt to a wide variety of manufacturing processes and business needs.
Best for:
Best for discrete manufacturers with complex workflows and multi-site operations who need real-time performance monitoring and quality management.
Key Features:
Real-time monitoring for production and performance
Advanced quality management tools
Multi-site support for large-scale operations
Integrated global financial management
Customizable workflows to match specific business needs
Deployment: Cloud & On-Premise
User Range: 10–Unlimited
Pricing: Starts at $125/user/month
Implementation Cost: $50,000+
Whether you're looking for an ERP solution that's easy to implement, offers deep customization, or integrates smoothly with your existing systems, there's an option out there to meet your needs.
Now, let's examine the key features that make an ERP system truly effective for your industry.
Must-Have Features in ERP for Small Manufacturers
While every manufacturer’s needs are unique, certain features are essential for ensuring that an ERP system meets the demands of growing businesses and helps them maintain operational efficiency.
Here’s a breakdown of the key functionalities to look for when evaluating ERP solutions:
Inventory Management
Effective inventory management is a key component for small manufacturers, allowing them to track stock levels in real-time. It prevents stockouts, reduces overstocking, and improves order fulfillment. Features like automated stock updates, barcode scanning, and batch tracking ensure that you always have the right amount of inventory available, without wasting precious resources.
Production Management
For small manufacturers, production planning and execution are critical to meeting deadlines and maintaining smooth operations. ERP systems help manage production schedules, monitor progress on the shop floor, and track work orders in real-time. Bill of Materials (BOM) management ensures that materials are available for production, while also offering shop-floor tracking features to monitor labor and machine performance.
Accounting and Financial Management
Managing finances is critical for any business, and an ERP system integrates financial management into the entire workflow. From invoicing and billing to tracking expenses and managing payroll, ERP systems simplify financial reporting and help maintain healthy cash flow. With accurate, real-time financial data, small manufacturers can make informed decisions and stay on top of their budgets.
Quality Control
Maintaining product quality is essential in manufacturing. ERP systems enable businesses to set up quality control measures at every stage of production. From raw materials to finished goods, manufacturers can track quality parameters and prevent defects from reaching customers. This feature also helps comply with industry standards and avoid costly recalls.
Order Management
Order management systems built into ERP software help manufacturers track sales orders from initiation to delivery. These systems ensure accurate order processing, reduce errors, and automate invoicing and shipping details. As a result, customer satisfaction increases, and businesses benefit from smoother operations.
Supply Chain Management
An efficient ERP system helps small manufacturers manage their entire supply chain. By integrating with suppliers and providing real-time data on inventory and production levels, ERP software enables timely procurement and reduces stockouts. This feature helps small manufacturers respond quickly to market demands and minimize disruption in production. Supplier synchronization and clear delivery timelines are key for smoother supply chain operations.
Cloud Access
With the rise of cloud computing, small manufacturers can benefit from cloud-based ERP systems that eliminate the need for physical servers. With cloud access, teams can manage operations from anywhere, using just a laptop or phone. Gartner reports that by 2025, over 85% of organizations will adopt a cloud-first strategy, making the cloud the foundation of new digital experiences.
User-Friendly Interface
An intuitive and straightforward user interface is essential for small manufacturers, especially for business owners who may not be technically savvy or have a large team. ERP systems with user-friendly interfaces ensure that employees, whether experienced or new, can easily navigate the system without needing extensive training, making the system more efficient from the start.
AI & Analytics
AI and analytics are becoming an essential trend in ERP systems for small manufacturers. These systems can predict demand, detect production blockages, and provide actionable insights that help improve operations. As more manufacturers accept technology, AI-enabled ERP solutions will continue to drive efficiency and cost savings in the long run.
With these features, small manufacturers can have a strong and scalable ERP system that meets their unique needs, manages operations, and positions them for growth. These tools are designed to make manufacturing operations more efficient.
Now that we've explored why ERP is essential for small manufacturers, let’s look at the key factors you should consider when evaluating an ERP vendor. This checklist will help you make an informed decision, ensuring that your ERP solution fits your business needs and goals.
Checklist to Evaluate a Manufacturing ERP Vendor
Choosing the right ERP vendor is a critical decision that can significantly impact your business. The ideal ERP system should not only meet your current needs but also be flexible enough to grow with your business. Here's a detailed checklist of essential criteria to help you make an informed decision when evaluating ERP vendors for your manufacturing business:
Functional Fit
Covers core manufacturing functions (production planning, inventory management, order tracking, quality control)
Supports industry-specific needs (e.g., reel management, dispatch scheduling for packaging/corrugation)
Aligns with your current and future operational requirements
System Integration
Integrates smoothly with existing systems (CRM, accounting, WMS, etc.)
Offers open APIs for easy third-party integration
Minimizes manual data entry and ensures seamless data flow
Customization Options
Allows modification of workflows and business processes
Enables custom dashboards and reporting tools
Supports feature enhancements as business evolves
Vendor Technology
Built on modern, scalable technology (e.g., cloud computing, AI, ML)
Provides real-time operational insights and analytics
Keeps up with evolving tech trends and industry demands
Implementation and Support
Offers a clear and structured implementation plan
Provides thorough onboarding and team training
Ensures ongoing technical support and troubleshooting
Has a reliable customer service and support team
Cost vs. ROI
Transparent pricing with no hidden fees
Includes total cost of ownership (software, setup, training, support, updates)
Demonstrates measurable ROI through time savings, error reduction, and efficiency gains
Vendor Experience
Proven experience in manufacturing ERP deployments
Familiar with industry-specific challenges and needs
Offers case studies, references, or testimonials from similar businesses
By evaluating these key criteria, you can confidently select an ERP vendor that not only meets your current needs but also supports the long-term growth and success of your manufacturing business.
"Now that you’ve evaluated the key criteria for selecting an ERP vendor, it’s important to consider your deployment options. One of the biggest decisions you’ll face is choosing the right ERP system. Let’s explore which option is best suited for modern manufacturers.
Cloud-Based vs. On-Premises ERP: What's Best for Modern Manufacturers?
When selecting an ERP system, one of the most significant decisions manufacturers face is whether to opt for a cloud-based or on-premises ERP. Both options come with their own set of advantages and challenges, so understanding their differences is essential for choosing the right solution for your business.
Cloud-Based ERP
A cloud-based ERP operates on a software-as-a-service (SaaS) model, where your ERP system is hosted and maintained by the vendor on their remote servers. With cloud ERP, businesses pay a monthly subscription fee for continued access, while the vendor handles system updates, patches, and maintenance.
Benefits of Cloud ERP:
Lower Upfront Costs: Cloud ERP typically requires a smaller initial investment since you don't have to buy hardware or worry about setup costs.
Automatic Updates: Vendors handle software updates and patches, ensuring your system is always up to date with the latest features and security enhancements.
Quicker Setup: Cloud-based systems are often faster to deploy, which means less downtime for your operations.
Scalability: Cloud ERP systems can easily scale as your business grows, offering the flexibility to add new features and functionalities when needed.
Security: While data is stored off-site, reputable cloud ERP vendors invest heavily in security, often providing better protection than small to medium-sized businesses could afford with on-premises solutions.
Accessibility: Cloud ERP allows you to access your system from anywhere, which is perfect for businesses with remote or travelling teams.
Disadvantages of Cloud ERP:
Data Security Concerns: Despite advanced security measures, some businesses might still be uneasy about storing sensitive data off-site.
Ongoing Subscription Fees: Over time, the recurring subscription fees can add up, potentially leading to higher long-term costs than an on-premises solution.
Limited Customization: Cloud solutions may not offer as much flexibility in customization compared to on-premises systems, particularly for businesses with complex or highly specialized processes.
Reliance on Internet Connectivity: Cloud ERP requires a stable internet connection; any downtime or connectivity issues could interrupt business operations.
Cloud ERP is a popular choice for small and medium-sized manufacturers seeking a flexible, cost-effective solution that can grow with their business, without requiring a significant upfront investment.
On-Premises ERP
On the other hand, on-premises ERP involves installing the ERP software on your company’s own servers and hardware. While this model is older, it still offers distinct advantages for businesses with specific needs.
Benefits of On-Premises ERP:
Greater Control: With on-premises ERP, your business retains full control over your data and systems, which can be a critical factor for industries that deal with sensitive information.
Customization: On-premises systems tend to offer more flexibility in terms of customization. You can tailor the software to meet your exact requirements, particularly if you have complex or unique manufacturing processes.
Long-Term Investment: Although the initial costs are higher, on-premises ERP can be a solid long-term investment, especially for businesses with dedicated IT resources to manage the system.
Data Privacy: For businesses that prefer to keep their data in-house and are concerned about third-party storage, on-premises ERP ensures that all data stays within your physical infrastructure.
Disadvantages of On-Premises ERP:
Higher Initial Costs: On-premises ERP requires a significant upfront investment in hardware, software, and IT resources for implementation.
Ongoing Maintenance: Your internal team will need to handle software updates, patches, and any hardware issues, which adds to the operational burden.
Scalability Challenges: Expanding or upgrading an on-premises system often requires additional hardware and manual intervention, which can be both costly and time-consuming.
Longer Deployment Time: On-premises ERP typically takes longer to implement, which can result in extended downtime during the setup phase.
While on-premises ERP offers flexibility and control, it also requires more investment in terms of both initial setup and ongoing maintenance, as your team will need to handle software updates, patches, and any hardware issues.
Which One Should You Choose?
The decision between cloud-based and on-premises ERP depends largely on your business's needs, growth plans, and IT capabilities. Cloud ERP is ideal for businesses looking for an affordable, easily scalable solution with minimal IT overhead. It's especially suited for smaller manufacturers or those with limited IT resources.
On-premises ERP, however, might be a better fit for larger manufacturing operations that require high customization, full control over their data, and have the resources to manage the system internally.
Ultimately, both cloud and on-premises ERP solutions can manage your manufacturing operations, but understanding their advantages will help you make the best choice for your company’s current and future needs.
But like any powerful tool, ERP systems don't come without their hurdles. Let's now take a look at the common challenges small manufacturers face during implementation and how to solve them before they slow you down.
Challenges and Solutions in ERP Implementation
Even with the right ERP solution, small manufacturers can still encounter challenges along the way. From system delays to hesitant teams, the path to successful implementation isn't always straightforward. But knowing what to expect and how to handle it can make a world of difference. Let's take a look at some common challenges and learn how to tackle them before they become costly roadblocks.
Resistance to Change
Change is tough, especially when teams are used to doing things a certain way. One of the biggest challenges in ERP adoption is internal resistance from employees who worry about learning new systems or losing control.
Solution: Start change management early. Talk to your team about why the ERP is being implemented and how it will make their work easier. Offer hands-on training and keep communication open throughout the process so that employees feel included, not blindsided.
Data Migration Headaches
Moving from legacy systems or manual records to an ERP is a big leap. If your data is disorganized or inaccurate, the ERP system can’t function properly, and it may lead to bigger issues down the road.
Solution: Audit your data before you move it. Clean it up, organize it, and run multiple test migrations to make sure everything transfers accurately. Involve someone who understands both your business processes and data structure to lead this phase.
Budget and Timeline Overruns
It’s common to underestimate how long ERP implementation will take or how much it will cost, especially for first-timers.
Solution: Set a realistic scope from the start and break the implementation into phases. Choose a vendor who’s transparent about costs and offers flexibility. Build in buffer time and cost for unexpected issues, and schedule regular check-ins to monitor progress.
Lack of User Training
Even the most powerful ERP system is useless if your team doesn’t know how to use it. Skipping proper training is a shortcut to frustration and low adoption.
Solution: Invest in role-specific training from the very beginning and continue offering support after go-live. Choose an ERP system with a clean, simple interface that’s easy to learn, especially for non-technical users.
Integration Woes
ERP systems often need to work with other tools your business already uses like CRMs, warehouse software, or even Excel sheets. Poor integration can cause gaps in data flow and efficiency.
Solution: Plan your integration strategy early. Choose an ERP solution that offers strong compatibility with your existing tools or APIs for custom integrations. Test all connections before go-live to make sure your systems speak to each other smoothly.
By addressing these challenges early with the right approach and tools, small manufacturers can avoid costly setbacks and ensure their ERP system delivers the value it promised from day one.
Conclusion
For small manufacturing businesses, investing in an ERP system isn't about keeping up, it’s about taking control. Whether you're struggling with disconnected spreadsheets, unpredictable inventory, or growing pains that slow you down, the right ERP can shift how your business runs day-to-day. But it's not a one-size-fits-all decision. What works for a large enterprise may be overwhelming for a small team. That's why choosing an ERP solution that aligns with your workflows, scale, and budget makes all the difference.
At SB Infotech, we don't just implement ERP; we customize it to your shop floor, team, and goals. Reach out today for a quick consultation or a personalized demo. Let's find the ERP that fits your business, not the other way around.
Comments